Business Process Analysis- The Complete Guide
Whether it is routine maintenance, the implementation of quality control guidelines, or following stringent food safety standards, in order to run an efficient operation, a business process analysis must be frequently performed.
A business process analysis requires a thorough examination of every aspect of a procedure, including all personnel that is involved and equipment that is used. Doing so will enable systematic delays to become evident, allowing for necessary adjustments to be made.
A Business Process Analysis and its Significance
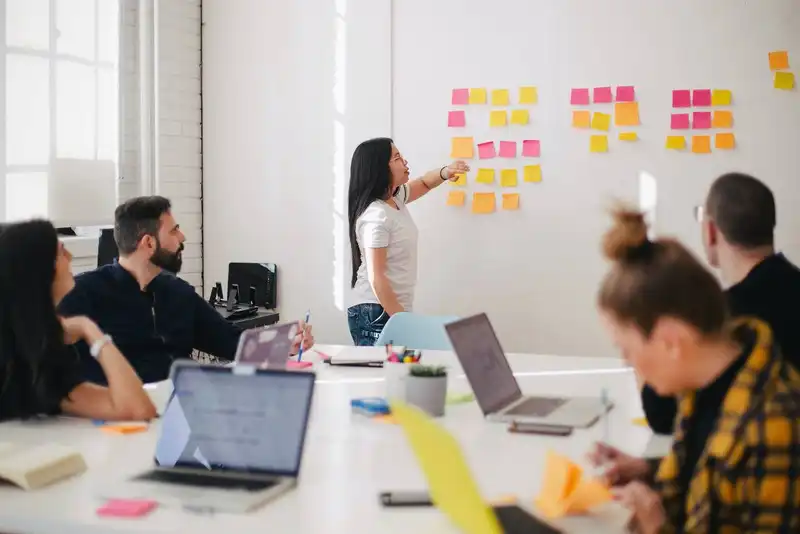
A business process analysis helps determine the effectiveness and efficiency of a procedure in accomplishing goals.
Comprehensively assessing a procedure will make it easier to identify the source of issues and delays within the system. With this knowledge, informed and data-driven decisions can be made to eliminate these setbacks.
Additionally, an analysis allows for cost reduction solutions and minimizes waste of resources. For example, outdated tools that may require frequent repairs or more energy usage can be removed when examining current operational processes. To ensure that existing procedures are not obsolete, businesses can update their methods with newer and energy-efficient technology.
Since a business process analysis encourages thorough screening into every part of standard procedures, it will highlight underperforming methods. By continually updating these systems with productive alternatives, businesses can re-organize and refine their methods to enhance performance and productivity.
A Guide to Business Process Analysis
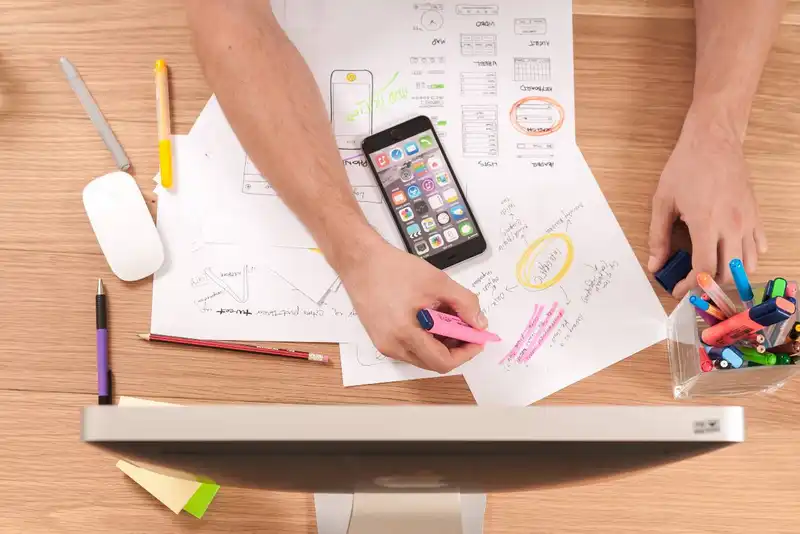
1. Identify Which Process to Analyze
For the first step, a process must be identified for analysis. Typically, business processes that are critical to operations, such as those that affect the quality of output, overall costs, and profits are emphasized and continually updated.
It is also important to analyze new procedures that have been recently implemented to monitor its effectiveness and whether or not it is functioning as intended. Additionally, existing unproductive methods should be reviewed to confirm or deny any uncertainties.
2. Compile Key Data
To accurately and properly conduct a business analysis, all information and data regarding the process should be collected. For example, data that relates to raw material sources, machinery, output quality, and procedural steps need to be compiled. Additionally, documentation about the process and employee testimony will also be conducive to analyze.
Organizations that use disparate systems for data should utilize reliable integration software to streamline the flow of pertinent information from different data sources.
3. Map the Business Process
At this stage, data should be compiled and transformed into visuals, such as diagrams, charts, and graphs. This is called business process mapping, which is a technique that creates visual depictions of business operations.
Visual analytics makes complex data more comprehensible. This will enhance accessibility and visibility of key factors, such as important stakeholders that are involved with the operation, risks within the process, and inefficiencies.
Reporting software simplifies this step, minimizing the need for a business analyst or data professional. These digital systems are integrated with cloud syncing, which allows for real time data assessment in a user-friendly format.
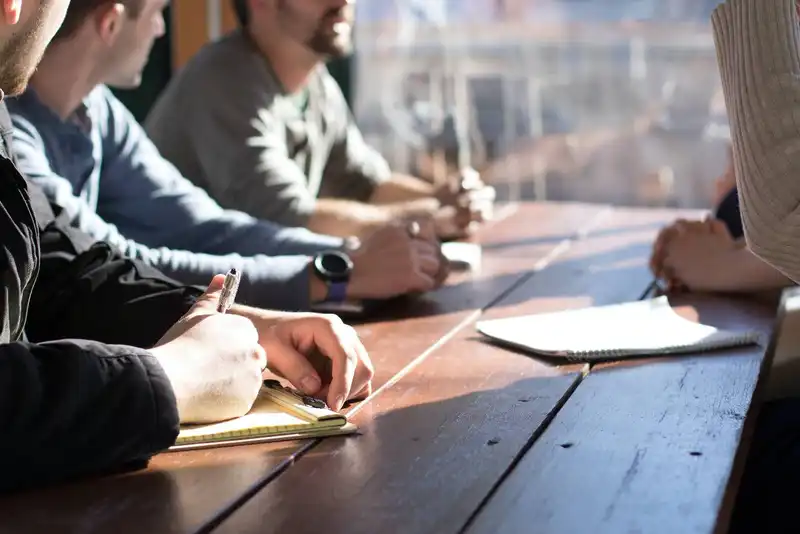
4. Analyze
With all of the information and data about the entire process collected and mapped out, proper and effective analysis of business procedures can be made.
When analyzing, consider pinpointing the key features of the process and whether it can be improved to maximize the operation's overall potential. It is also helpful to identify what causes delays or problems within the process and to assess the source of these issues.
In addition, to improve profitability, data should be used to detect what part of the process causes waste of resources and whether there are cost-effective alternatives.
5. Outline Improvement Plans
After analyzing, it will be easier to comprehend how a business process operates and what can be done to make it more efficient and proactive.
At this stage, solutions should be tailored to the issues that were detected. These adjustments may be minor or they may require an entirely redesigned process, depending on the issue at hand.
There are various plans for changes that should be considered, such as business process management. This refers to an ongoing series of long-term actions intended to maintain and enhance business procedures.
Another alternative is business process improvement, which is a method for remedying inefficiencies by remodeling a specific system. This is typically performed to minimize the time it takes for the course of action to be completed, boost high-quality output, and reduce waste.
Once improvements have been made, all operations should be continually monitored and a business process analysis must be frequently conducted. This will ensure that new changes are working as intended and are productively contributing to attaining goals.