How to Reduce Production Costs
There are all sorts of costs that arise when producing goods or providing services. If production costs are too high, it is difficult for a company to turn a profit, which is why it's imperative to maintain low production costs while still maintaining quality.
To properly manage expenses, determine whether labor, material, and overhead costs exceed budget. Here is an overview of typical production expenses and the best cost-saving practices to combat them.
Two Key Questions to Ask Before Getting Started
1. Is the Production Cost the Same as the Manufacturing Cost?
Both the production cost and manufacturing cost are utilized to gauge the total cost of production.
Production costs refer to all of the expenses incurred from manufacturing a product or providing a service. Examples of production costs include advertising expenses, marketing costs, equipment needed for production, and supply purchases. Production costs are typically fixed, meaning they do not change regardless of the number of goods and services produced.
Manufacturing costs refer to only the direct expenses required to create a product or service. Examples of manufacturing costs include the price of materials, labor costs, and overhead expenses. Manufacturing costs fluctuate depending on how many products or services are produced.
2. How Does the Company Calculate the Total Cost of Production?
To calculate the total cost of production, add the fixed costs and the variable costs-
Total Cost of Production = Fixed Costs + Variable Costs
The cost of production per unit is a breakdown of the fixed and variable costs incurred from creating a single product or service. Here is the equation to calculate the cost of production per unit-
Cost of Production Per Unit = Fixed Cost + Variable Costs / Number of Units
Elements of Production Costs
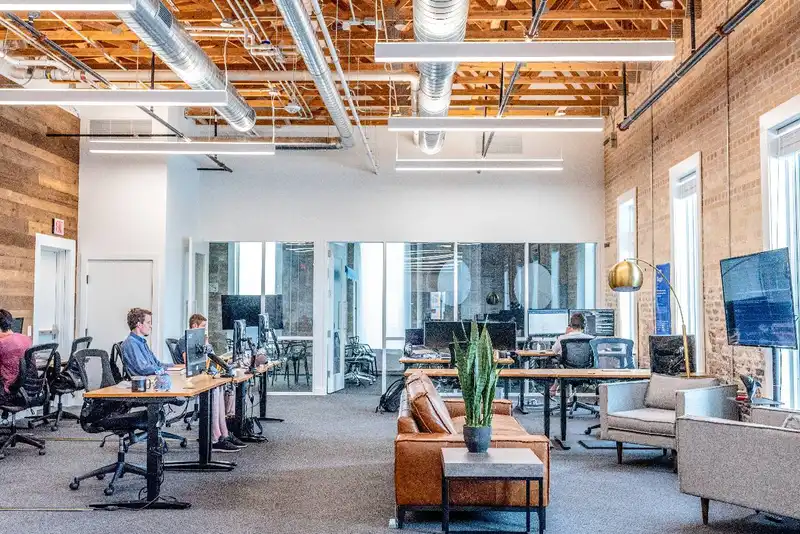
Monitoring the various elements of production helps reduce costs without sacrificing the quality. The various production costs include-
Labor
Labor costs includes wages, healthcare, insurance, and any other benefits owed to employees.
Raw Materials
Any materials utilized to manufacture a commercial product are also a production cost. Examples include steel, oil, forest resources, glue, plastic, minerals, natural gas, or other consumables.
Machinery
Machinery is any equipment needed to install, move, or build a product during the production process. Examples include drill presses, cement mixtures, forklifts, rock crushers, hot steel rolling machines, and band saws.
Energy
Energy costs include energy sources utilized to run the production facility. In addition to Examples include utilities, gasoline, oil, coal, space heating, central cooling systems, or security lighting.
Types of Production Costs
Tracking the types of production costs helps stay on budget and keep expenses low. It also promotes growth and increases cash flow. Different types of production costs include-
Fixed Costs
Fixed costs are constant regardless of the number of products produced. Examples are insurance payments, property taxes, annual salaries, interest expenses, and some utilities.
Variable Costs
Variable costs fluctuate as the quantity of produced products or services changes. Examples of variable costs are costs for raw materials, labor costs, utilities, and sales commissions.
Fixed Costs and Variable Costs Combined
As production increases, both fixed and variable costs will also increase.
Growing businesses will usually change their cost structure, or the types and proportions of fixed and variable costs incurred. For example, a company may need to open a new production facility, increasing energy costs, machinery expenses, raw material costs, and labor costs.
An expanding business should continue to calculate how much production volume is needed to maintain or increase its gross margin and cover any newly incurred costs.
The Difference Between Production and Manufacturing Costs
Manufacturing costs only refer to the indirect and direct expenses involved in turning raw materials into a sellable product or service. Material and labor costs are direct expenses, while electricity utilized in the manufacturing facility is an example of an indirect expense.
On the other hand, production costs reflect all of the expenses associated with producing a product or service. Production costs include rent, the advertising budget, and business equipment.
10 Ways to Promote Cost Reduction
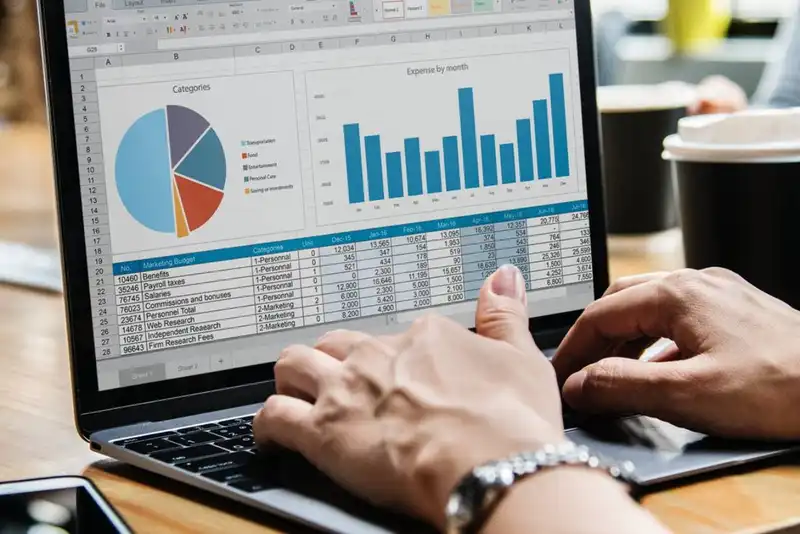
Here are 10 of the best ways to reduce production costs.
1. Reduce Supply Costs
Find suppliers that offer the best quality of materials at the lowest wholesale price. Don't be afraid to ask for a discount if utilizing a regular supplier. Research other suppliers to see if they offer better prices and use that as a bargaining chip to negotiate with a current supplier.
2. Save Money on Insurance
Work with an insurance broker to receive the best rates possible. Increase deductibles or ask for a discount when installing any new insured equipment, such as a security system, fire alarm, or set of water sprinklers.
3. Talk to an Accountant
Talk to an accountant to make sure that allowable business expenses are listed, which are common and accepted in a trade or business according to the IRS. Many allowable business expenses are eligible for a tax deduction which helps save money in the long-term.
4. Utilize Technology
Take advantage of low-cost software to manage inventory, sales data, and employee information. This helps free up valuable time and resources.
5. Optimize Space
Negotiate lease terms with the landlord to see if it's possible to operate a portion of the business from home. This will save money on rent and utilities.
6. Modernize Marketing Efforts
Invest in digital marketing to increase sales and afford production costs. Digital marketing is a relatively inexpensive advertising method that utilizes online-based technologies for marketing.
7. Increase Employee Productivity
Offer paid leave, retirement plans, and benefits that appeal to workers. Increasing employee job satisfaction levels is directly correlated to an improvement in productivity and a lower turnover rate. Maintaining low turnover is crucial, as the price to pay to hire new employees is costly and time-consuming.
8. Keep in Mind That Quality is More Important Than Quantity
Make sure to focus on the quality of products and services rather than how much output there is. Customers return because the quality of the product or service is superior to the competition.
9. Reduce Company Vehicle Expenses
Buy used cars to save money and lower insurance premiums. Utilize fuel-efficient vehicles that are less expensive to maintain.
10. Utilize a Spreadsheet to Manage Production Costs
Make sure to log production costs regularly on a spreadsheet or software database to track how much is being spent and where the funds are going.
Conclusion
Estimating the cost of production is essential to manage cash flow and eliminate unnecessary spending. Reducing production costs results in more available money to innovate, grow, or save for contingencies.
Businesses have the option to lower prices and pass on their production cost savings to customers. Lower prices can increase the demand for products, resulting in more sales. The company can also offer staff bonuses or an increase in pay to improve employee satisfaction levels.